THE ACCUTHRIVE Promise
You need the right blades to execute your vision. Our portfolio of high-performing medical blades has been perfected over decades and are trusted every time. AccuThrive’s blades are engineered with the precision to handle even your most challenging cases.
Because when patients are counting on you, you can count on us.
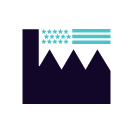
Blades manufactured in the U.S.A.
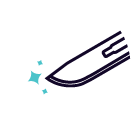
Consistent top-quality blades
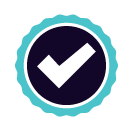
Highest standards for safety and quality control
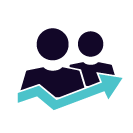
Innovation through collaboration
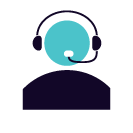
Exceptional customer support
A Tradition of Excellence
Since 1875, when Star Razor sold its first safety razor, our company has been built on innovative design engineering. The Kampfe Brothers’ Star Razor was such a success, it prompted Oliver Wendell Holmes, Sr., whose son would one day become a justice on the U.S. Supreme Court, to describe the razor in an article published in The Atlantic .
“This little affair had a blade only an inch and a half long by three quarters of an inch wide. It had a long slender handle, which took apart for packing, and was put together with the greatest of ease. It was, in short, a lawn-mower for the masculine growth of which the proprietor wishes to rid his countenance. The mowing operation required no glass, could be performed with almost reckless boldness, as one cannot cut himself, and in fact had become a pleasant amusement instead of an irksome task. I have never used any other means of shaving from that day to this.”
Since the company’s origins as Kampfe Brothers, and later making blades as part of American Safety Razor and Energizer Corporation, we have never strayed from our core focus of engineering and manufacturing the best high-performance blades and tools. In 2015, we began manufacturing and selling our own products under the name AccuTec and now, our clinical blades under the AccuThrive name.
Today we continue to provide our customers with specialty blades that improve efficiency and quality so that you can best serve your patients. At every step—from concept to customer delivery—we continue this tradition that reflects the best in American invention and ingenuity.
Not All Blades Are Created Equal
There’s much more to a blade than meets the eye. Every dimension—from cutting angles, metal hardness and durability to edge sharpness, size and configuration—is engineered to perform a specific function. This functional integrity of each blade type is key to our competitive advantage—when the cuts are cleaner, the end product is of higher quality. Manufacturing high performance blades is a craft: blade quality depends on the specification and quality of the raw material, the engineering of coatings and edges and the skill of the craftsman. In the end, the real test is how the blade performs on the job at hand.
It Begins with Steel Quality
We manufacture blades from carbon and stainless steel that perfectly balance requisite hardness and sharpness for the application at hand. All of our surgical, microtome and double-edge blades are made from stainless steel, which incorporates chromium to prevent corrosion. All materials must meet our specifications and standards and pass strict testing protocols before use.
Our Edge Gives You the Edge
Blade edges must not only be sharp, but sharp at the right angle and made with the right number of facets. The ideal edge design varies with the task at hand. We engineer blades to increase your productivity.
Blade Coating Reduces Cutting Friction
We bring mechanical, physical and process engineering expertise to every detail of blade manufacturing—and edge coatings are the important finishing touch. Our medical blades undergo a rigorous three-part process that creates a more durable cutting surface that provides reduced cutting friction. After a thorough preparation we apply a hard coating. A low-friction polymer top layer is vapor-sprayed to complete the process. Very thin surface coatings increase wear resistance and reduce friction at the tip. Each coating is customized for the intended cutting application.
Testing at Every Step of Production
We conduct tough physical and mechanical tests of steel properties throughout the production process. Controlled heating and cooling processes harden and improve steel properties to the precise requirements of each blade type. This microstructural combination of soft and hard surfaces ensures that each blade is engineered to perform at the tightest tolerances. Before and after metal perforation, heating, grinding, surface processing, cleaning, packaging, and shipping—all along the production line from start-up to mid-run to end of run, each blade is tested and retested.
Consistent Performance
There’s a direct relationship between blade performance and surgical outcomes. Higher quality blades that last longer mean fewer changeouts during surgery and less time in the O.R. Blades that cut through tissue with the least resistance mean less tissue tear for patients and less chance of scarring.
Commitment to Quality
Our expertise has earned us the following industry qualifications:
- ISO 9001: Demonstrating our sound quality management system and a focus on meeting customer expectations and delivering customer satisfaction.
- ISO 13485: Demonstrating that our quality management system is compliant with regulatory requirements for medical devices.
- American Standards for Testing Materials International: The sharpness of our blades set the international ASTM F2992-15 industry standard for cut force resistance.
We are actively planning for what our customers will need in the years to come. We recognize that new ideas inspire new opportunities, and that success promotes success. It is in this spirit that we offer you, our valued customers, our expertise, experience and exceptional blades.
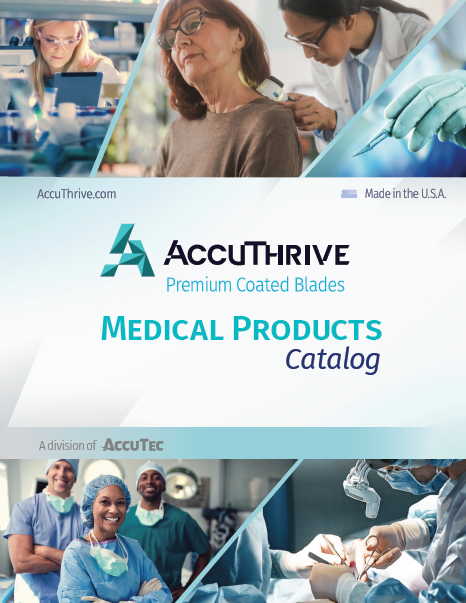
The AccuThrive Difference
We have more than a century of blade-making expertise. We focus on each aspect of blade development and adhere to strict quality standards throughout the manufacturing process.
Our Manufacturing Process
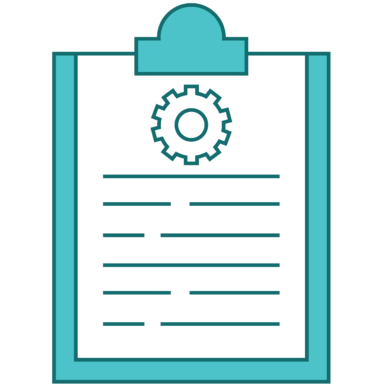
Raw materials inspection
Inspect raw materials (stainless steel) to ensure delivery as ordered and without defects
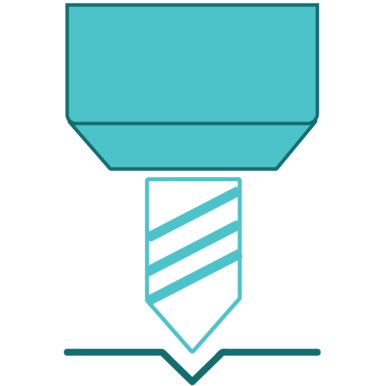
Perforation
Steel is perforated into specified blade shape
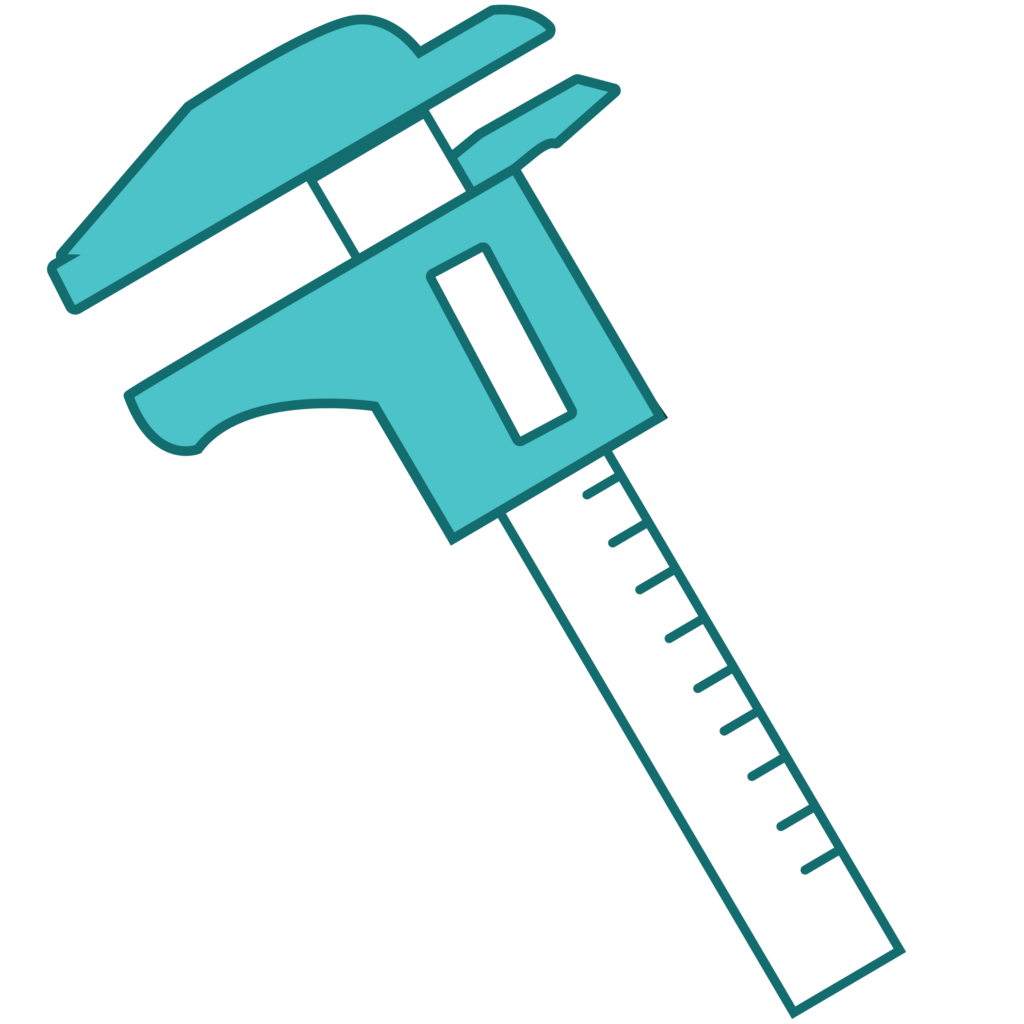
Dimension and profile verification
Quality checks ensure blade dimensions meet manufacturing specifications
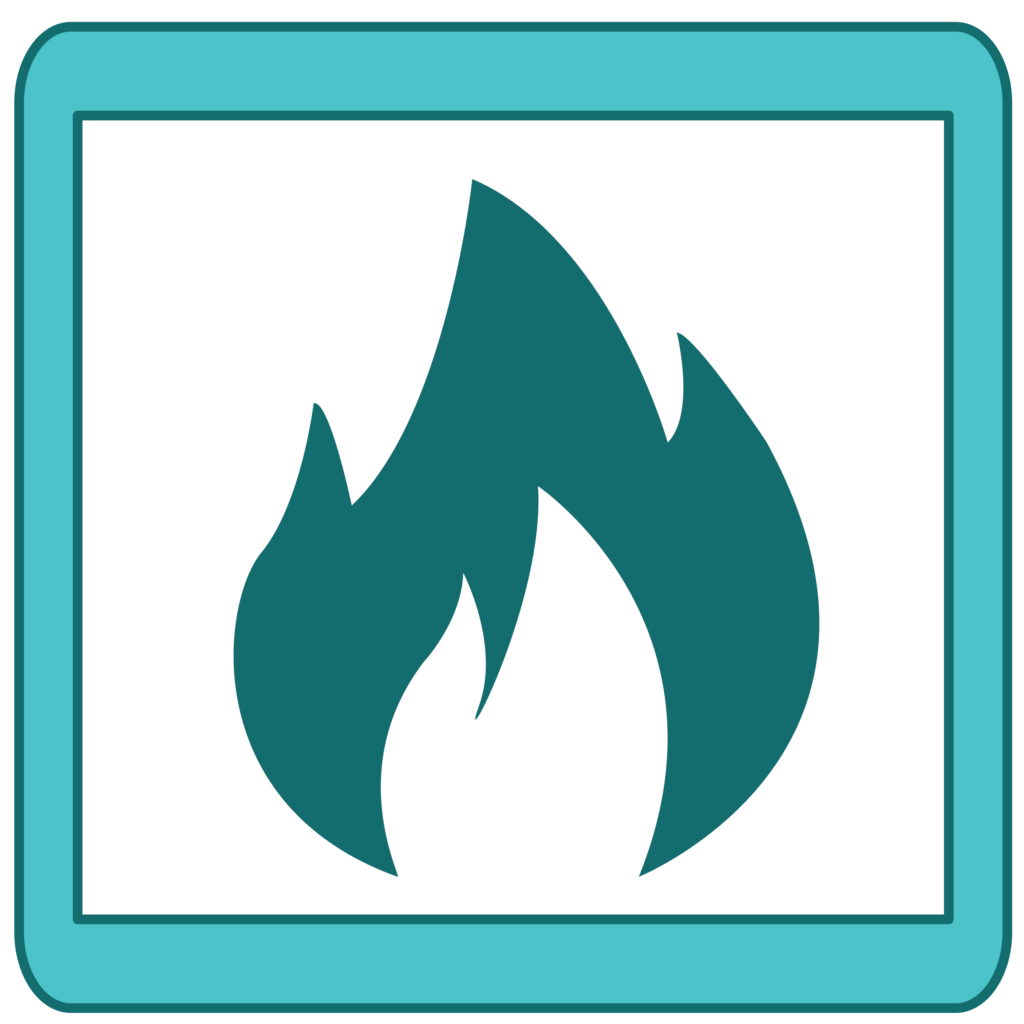
Heat treatment
Steel undergoes high heat to harden the metal
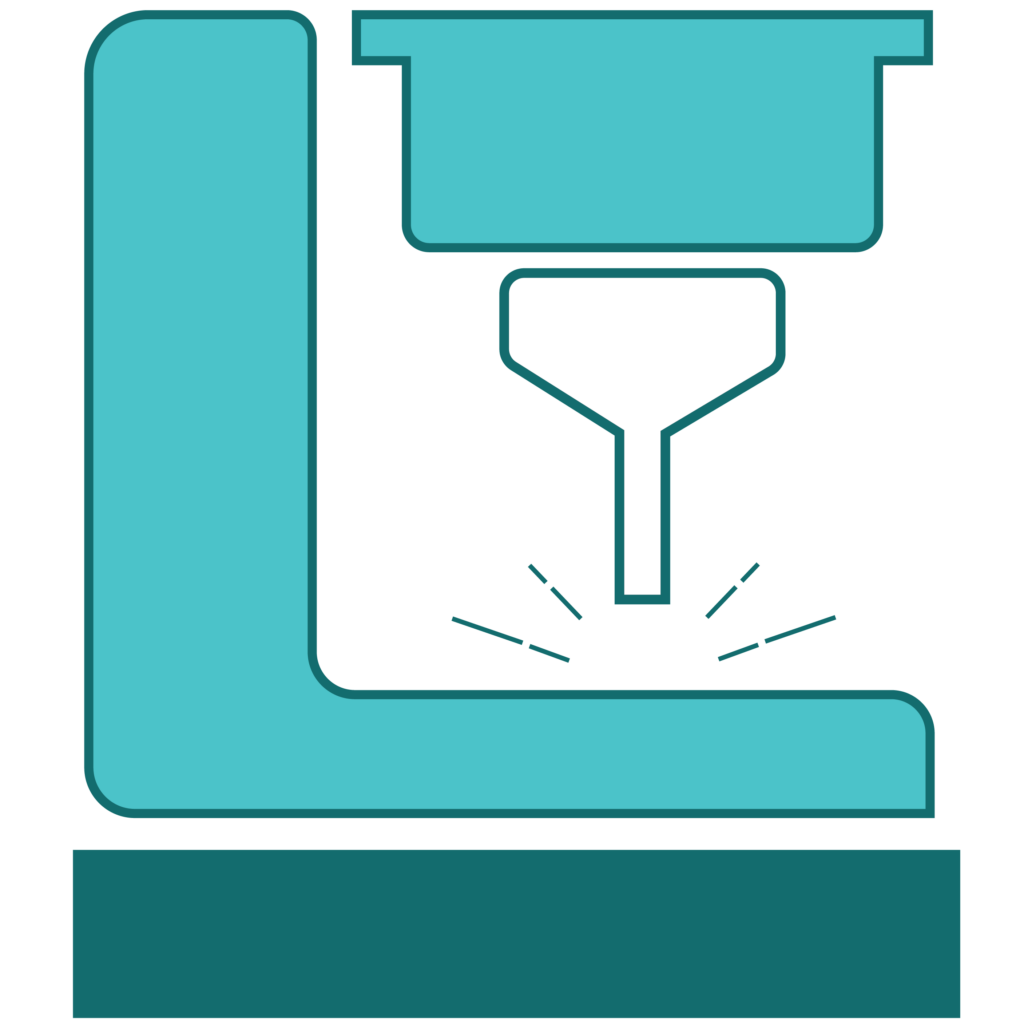
Hardening specifications check
Quality check to ensure each blade is hardened to manufacturing standards
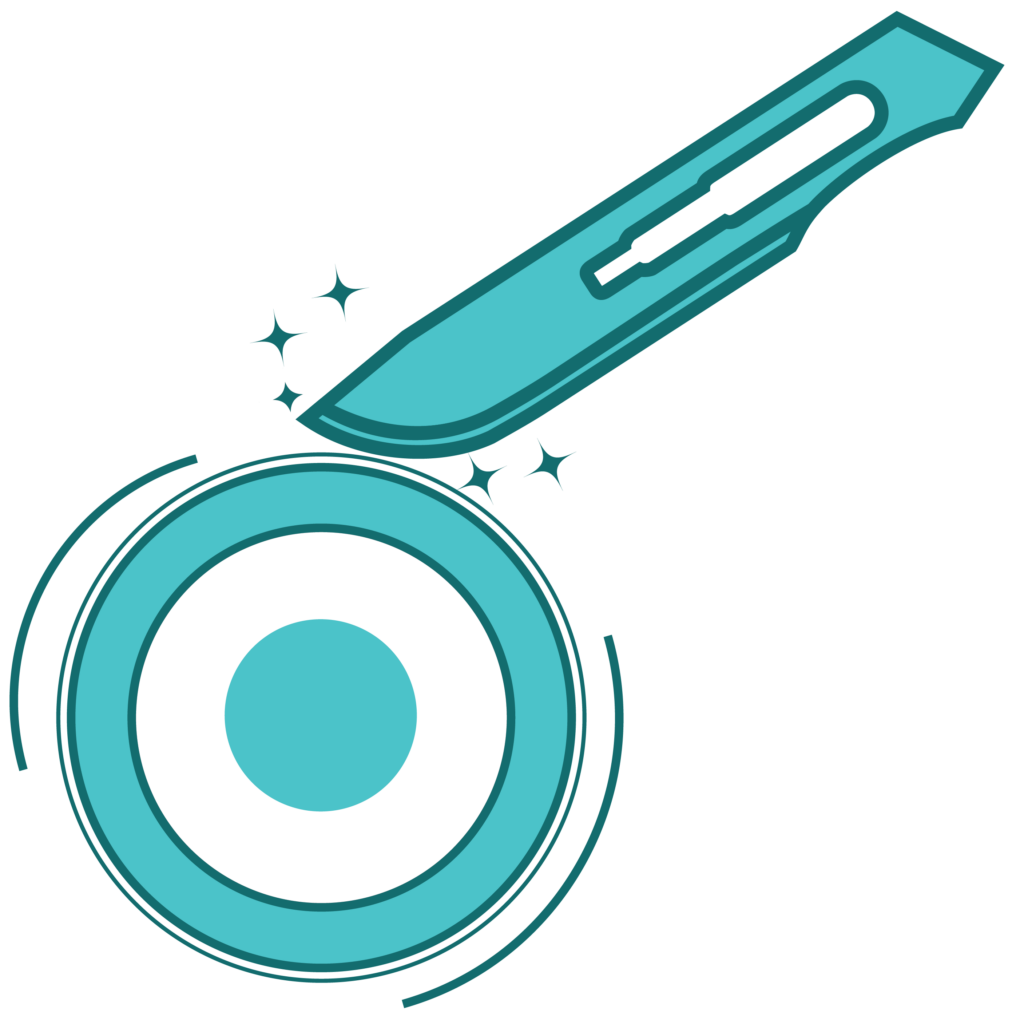
Grinding
Each blade edge is precisely ground into a two or three facet blade edge, depending on the blade’s function
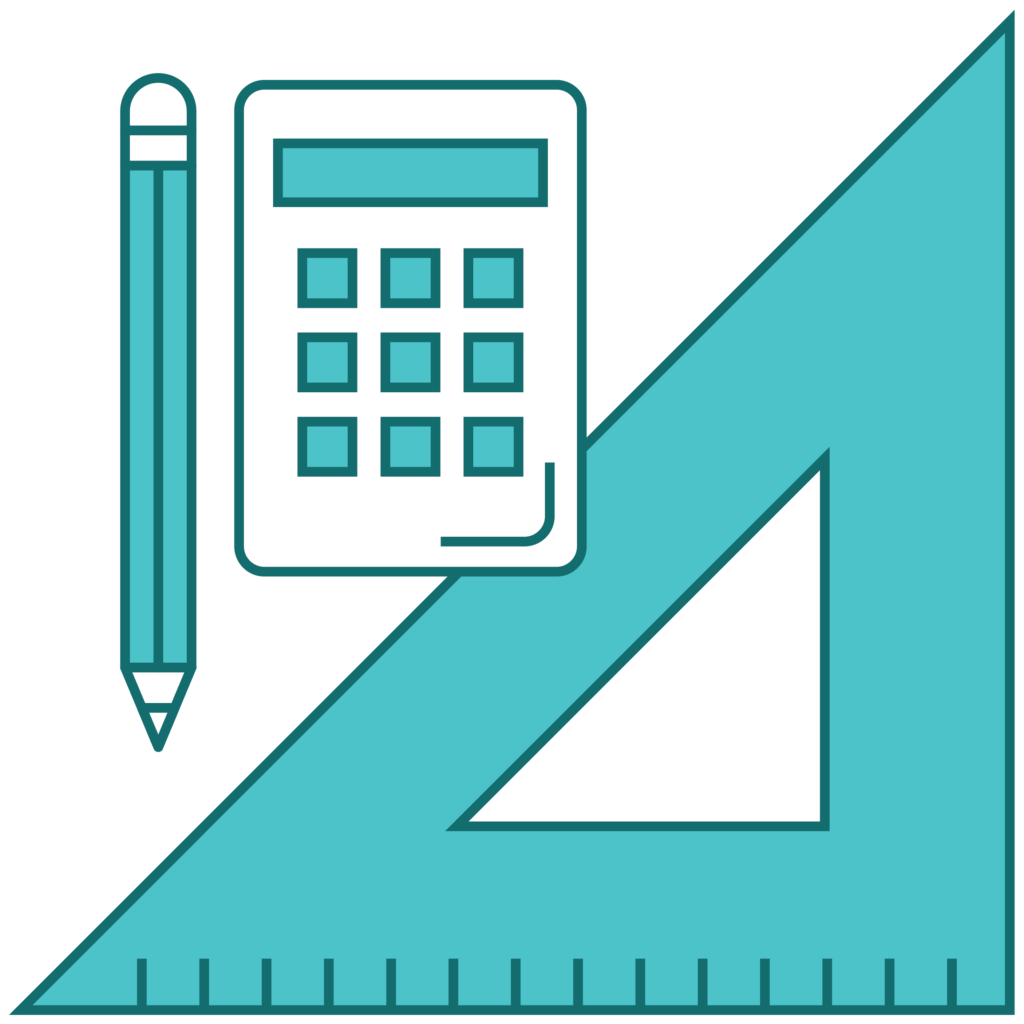
Edge dimensions and performance review
Quality check of blade edges under a microscope and performing initial cut force testing
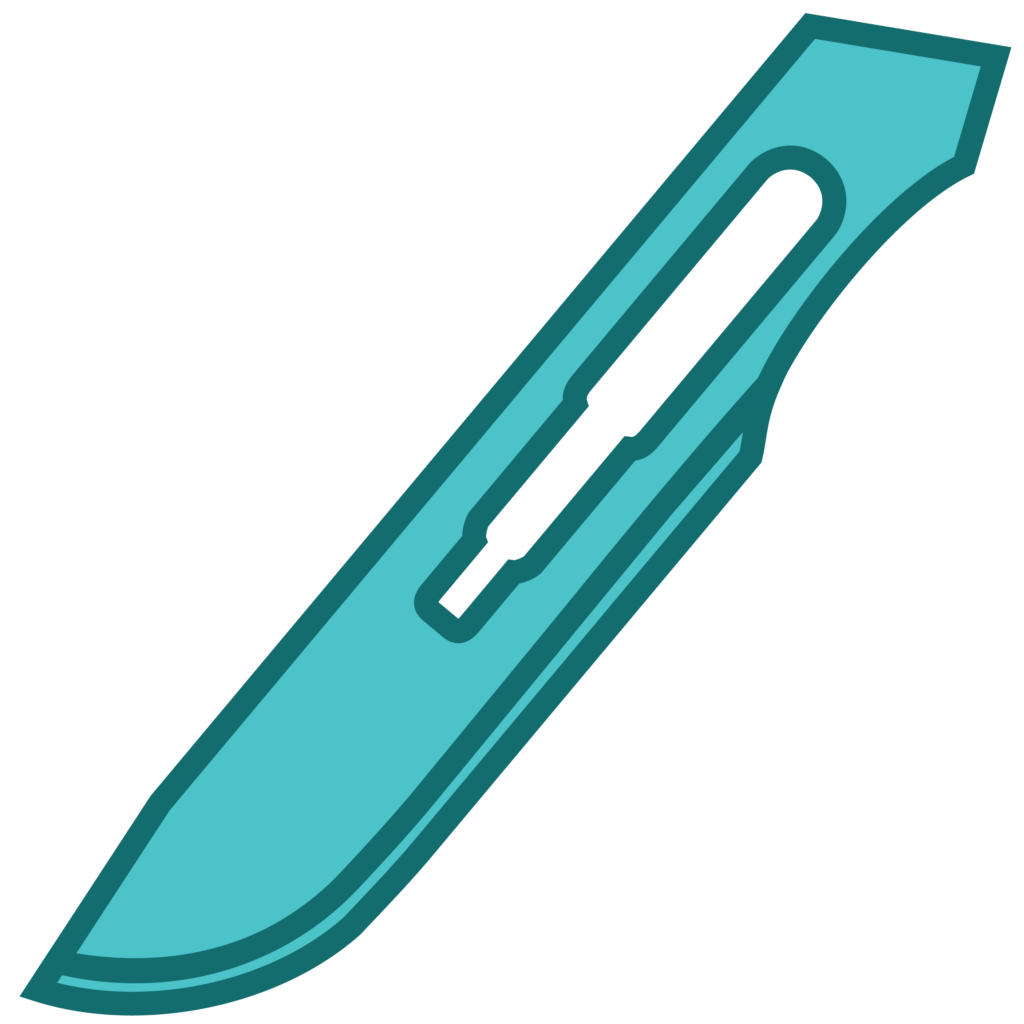
MicroCoat® enrichment
Coating the blade edge with MicroCoat, a proprietary technology designed for a smooth and resistance-free incision
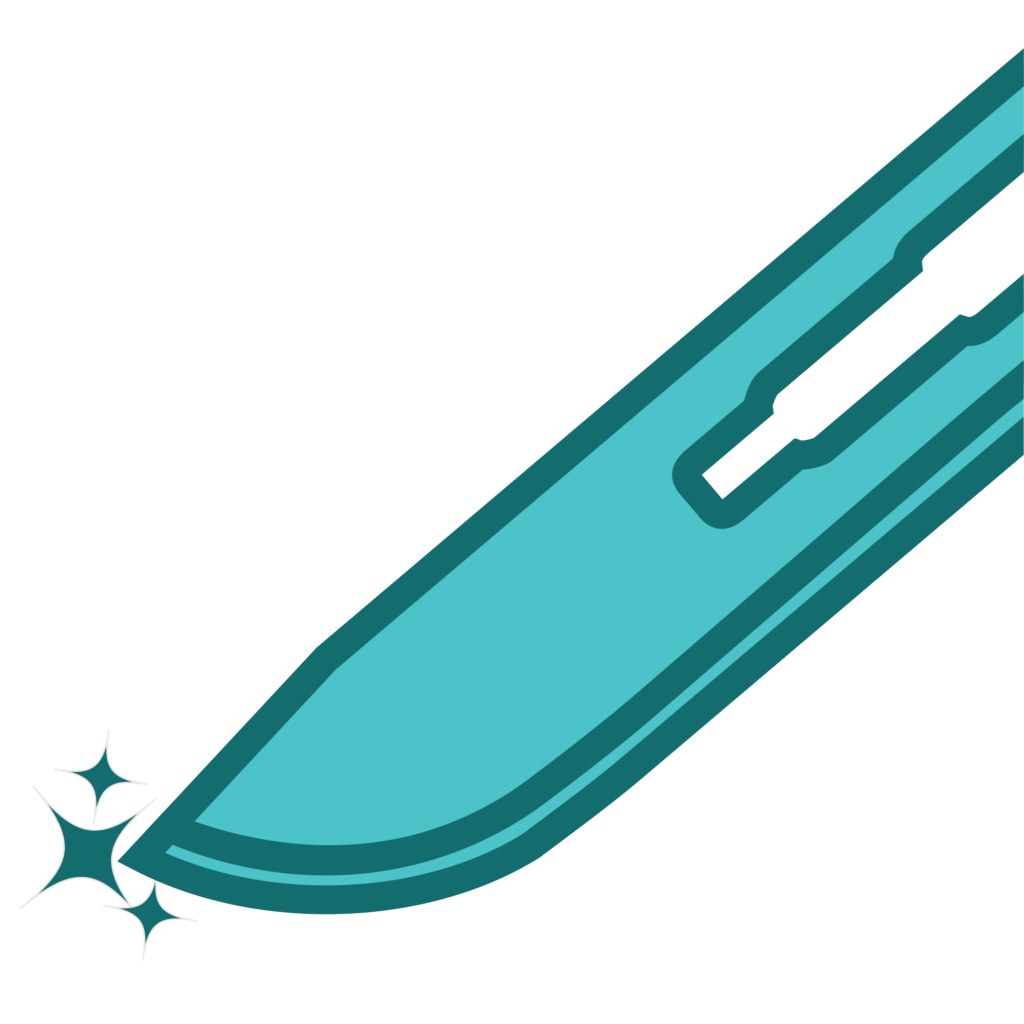
Blade testing
Enhanced blade performance testing to ensure blades are of the highest quality
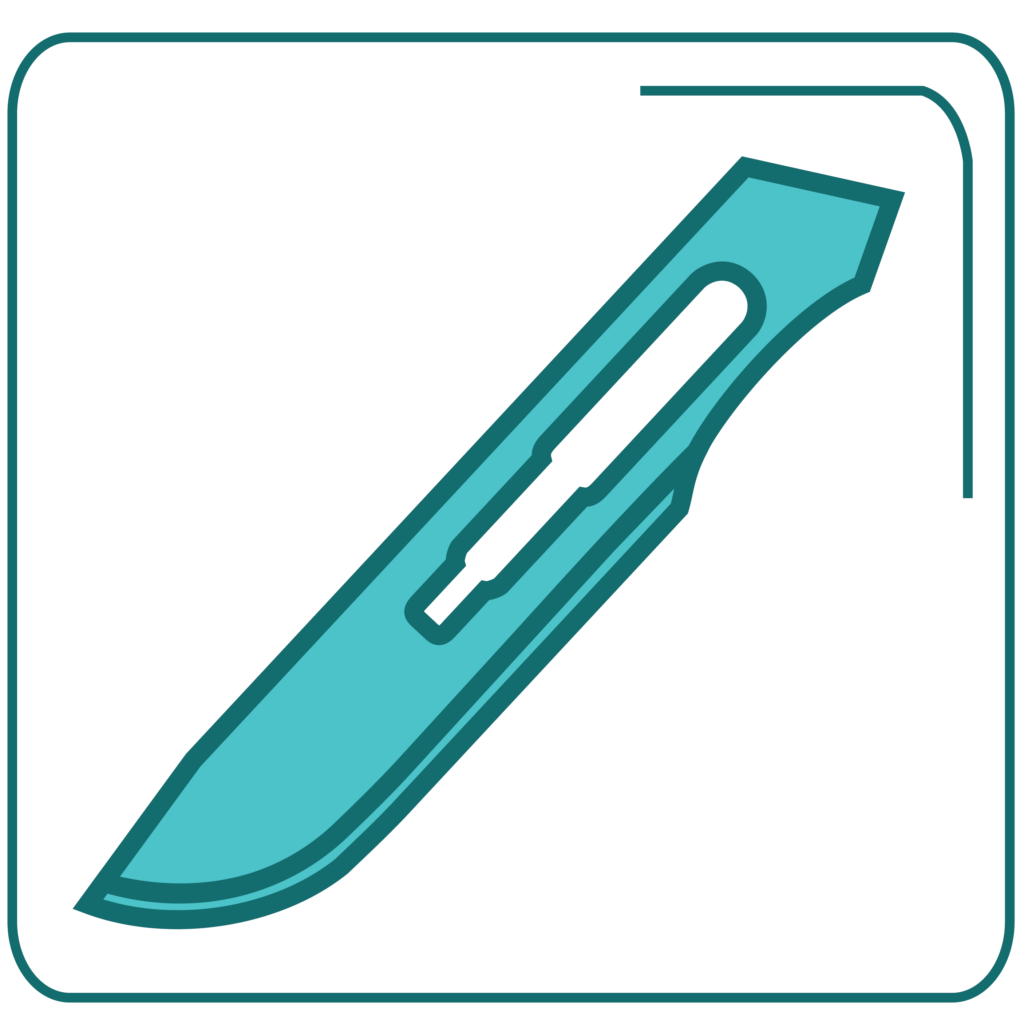
Finished blade
Blades are ready for shipment